Research
My research approach emphasizes exploiting physical insights by using mathematical, computer modeling, and experimental verification of different systems.
Current Projects:
Design for Additive Manufacturing
The current design process has been conceived within the constraints of a world where advanced AM (Additive Manufacturing) did not yet exist. This research focuses on the philosophy and practice of the design style that makes best use of the features and capabilities of AM, without neglecting that a big fraction of the concepts within traditional design still holds true. It reviews the rules, methods, software, and tools to assist a designer in understanding the design freedom allowed by AM and aiding the designer in exploring the open design spaces with less or no constraints.
This work studies the efficiency of AM from a strategic and operational point of view, the AM attributes in terms of cost, rate, flexibility, and quality. This research consists of (i) AM materials processes and applications (ii) Implicit modeling, (iii) Topology optimization, (iv) Design for lattice structures, (v) Part consolidation, (vi) Design support, and (vii) Quality assessment of a printed part.
I study the engineering aspects and physical principles of available AM technologies and their applications. I review the recent developments in this technology and the criteria needed to successfully select an AM technology for a particular design, discussing material compatibility, interface issues, and strength requirements.
In this work, the concept of implicit modeling which is different than regular CAD feature-based (faces, edges, lines, points, curves, and surfaces) modeling approaches are studied. Most CAD systems cannot deal with lattice structures, such as the example shown here, where you have thousands or millions of features.
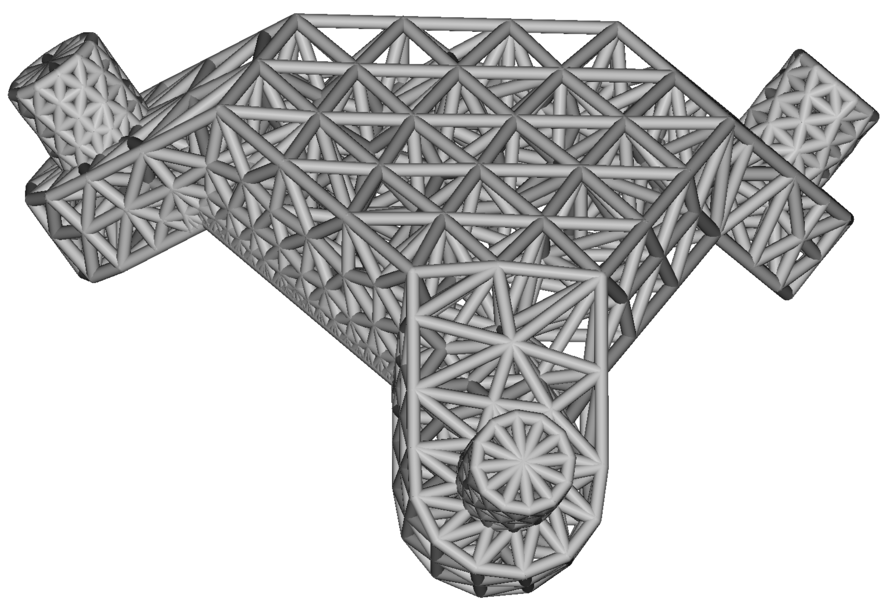
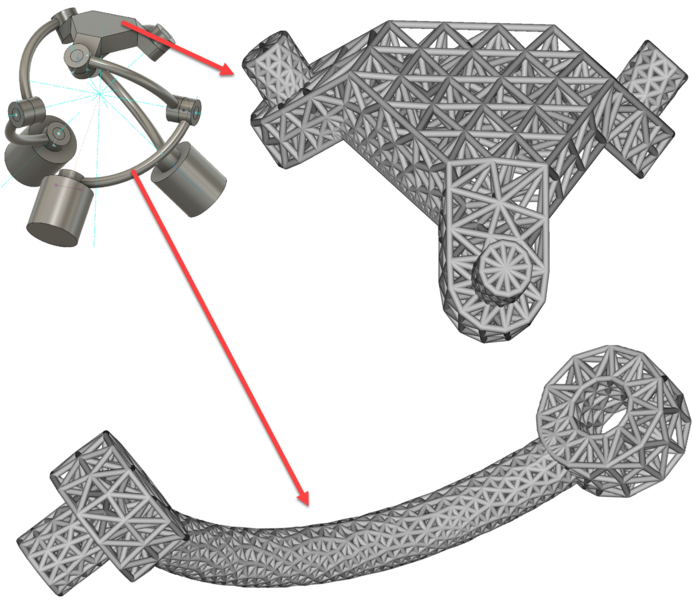
Topology optimization, a technique that can optimize material layout within a given design space, with an eye to AM capabilities, is active research. I also teach designers how to take advantage of the unique capabilities of AM processes which provide great design freedom to use lightweight cellular/lattice structures.
I will teach designers how they may redesign an object such that it has fewer parts with substantially different boundaries and connections. So, it may no longer need to be an assembly at all. In traditional manufacturing methods, some complex components are usually separated into several parts for the ease of manufacturing and then are assembled together. But complex part can be fabricated by AM in one shot.
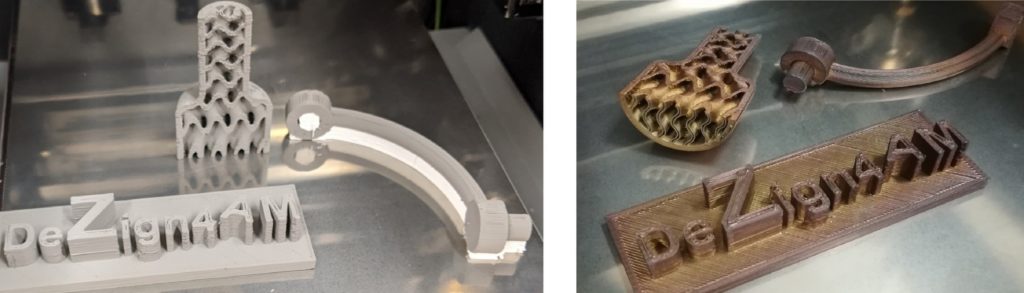
Advanced in Metal Additive Manufacturing has revolutionized the design and manufacturing of heat exchangers with complex internal structures. In an experiment, I designed a simple method to test the efficiency of heat exchanging for a small device with an internal optimum gyroid structure, made from Aluminum-Bronze alloy. We 3D printed 15 systems with the internal gyroid structure and compared their heat transfer coefficient with a standard system (no internal structure). Here is an image of one example of the printed parts (far right image, one sample after being cut in half for inspection).
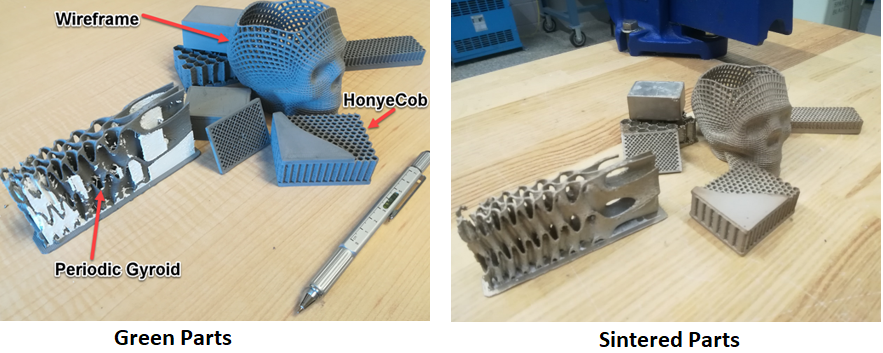
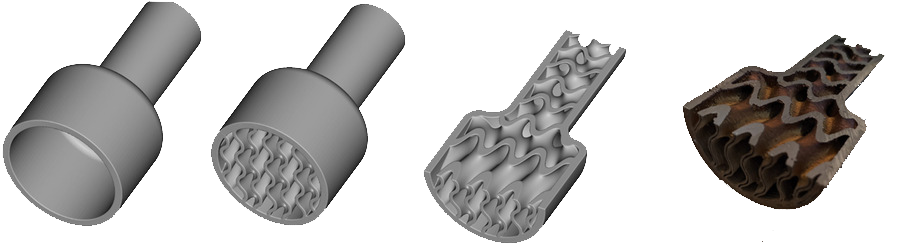
The experimental data confirmed the system with an internal gyroid structure is more efficient. It showed the mean heat transfer coefficient of the gyroid system exceeds the regular system by about 15%. I have ongoing research on how to apply this technique in the design of complex internal passages for heat exchangers on fluid distribution systems. There are a plethora of other applications of AM in human implants made of lattice structures that can enhance osseointegration in the biomedical field.
I will teach designers how they may redesign an object such that it has fewer parts with substantially different boundaries and connections. So, it may no longer need to be an assembly at all. In traditional manufacturing methods, some complex components are usually separated into several parts for the ease of manufacturing and then are assembled together. But complex part can be fabricated by AM in one shot.
One of my active projects involves methods to evaluate a metal-printed part in terms of its strength, hardness, toughness, and fatigue life. I use different techniques to check the physical and mechanical properties of a printed part. While tremendous design potential with AM technologies waiting for designers to explore, there is one big caveat. They need good CAD modeling approaches to support their exploration. Current CAD techniques are less than ideal for taking advantage of the unique capabilities of AM in creating novel shapes and structures.
Non-Destructive Testing for Additive Manufacturing
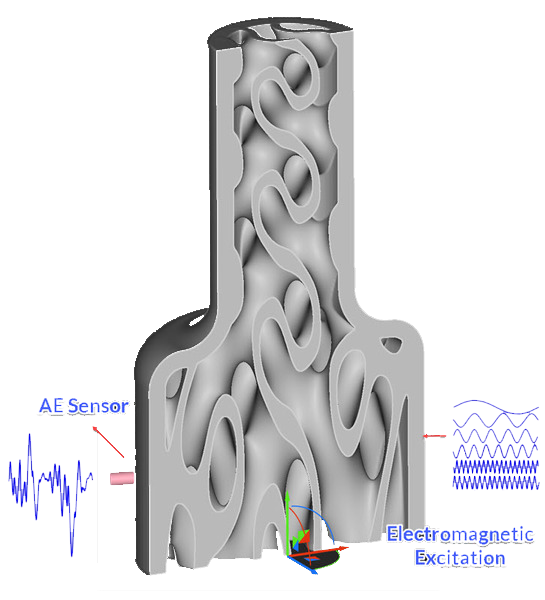
Application of AI in Manufacturing Processes
This research reviews core issues necessary in the application of ML (Machine Learning) and AI (Artificial Intelligence) in Manufacturing. I will study how AI can perform quality control, perform predictive maintenance, reduce environmental impact by cutting down materials waste, improve production, eliminates the need to program movements of a robot by using the CAD models. Research focuses on how in manufacturing, with AI adoption, industries are able to make rapid, data-driven decisions, optimize manufacturing processes, minimize operational costs, and improve the way they serve their customers.
Quality checks – Machines can be equipped with cameras to detect defects on the production line and spot any imperfections.
Prediction of failure modes –With enough data on how products are tested and how they perform, AI can identify the areas that need to be given more attention in a product test.
Predictive maintenance – Predictive maintenance predicts when machines need maintenance and prevents unplanned downtime by using machine learning.
Environmental impact – AI can help to transform manufacturing by reducing waste and its environmental impact and optimizing energy efficiency.
Making use of logistics data –AI can benefit manufacturers in supply chain management, risk management, predictions on sales volume, product quality maintenance, prediction of recall issues.
Unprogrammed Robotics – AI-Powered robots can interpret CAD 3D models, which eliminates the need to program their movements.
Monitoring of Pulp Refiner
I am a member of API (Advanced Papermaking Initiative) scholars. Learn more……
There are two main approaches to separating wood fibers: chemical refining and mechanical refining, and the application of each method depends on lignin. Lignin is an amorphous phenolic polymer responsible for holding wood fibers together. In a chemical refining a chemical process is used to dissolve lignin and separate fibers, but it also dissolves the fibrous material. Mechanical refining involves mechanically breaking the wood fibres apart from one another. In mechanical refining, therefore, the lignin remains. There are several types of mechanical refiners, including single disc, double disc, twin, and conical refiners.
Currently there is not any monitoring system that informs when to change the blade (plates) in a refiner. The downtime for changing the blades inside a pulp refiner marks one of the most critical machines in a pulp mill as a production bottleneck. Changing the blade with fresh ones is inevitable, but when it comes to the question of the optimum time for changing the blades, the answer is vague. Besides, the clearance between the blades is a critical parameter which affect the quality of fiber.
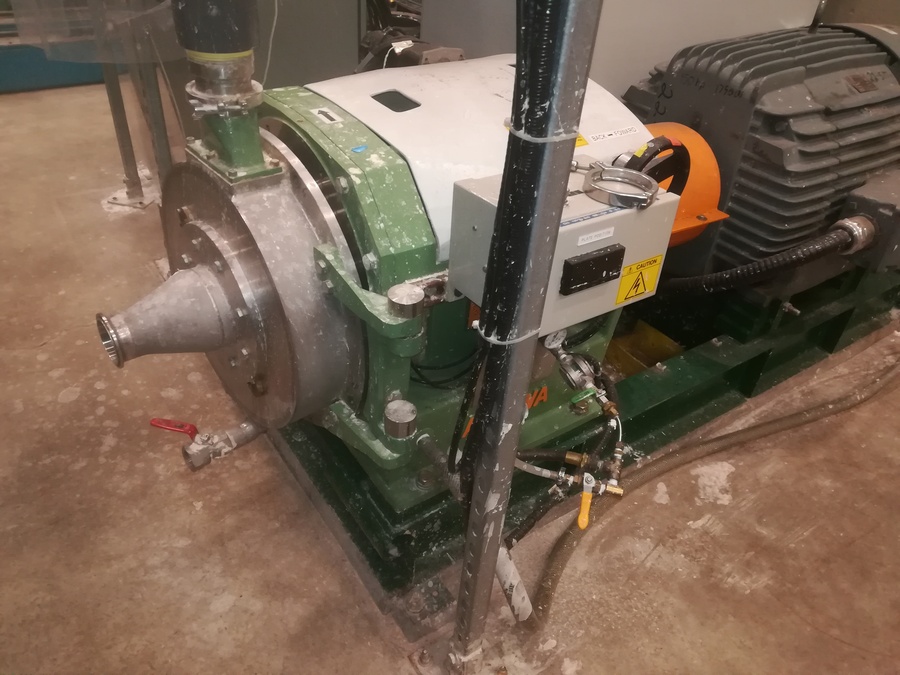
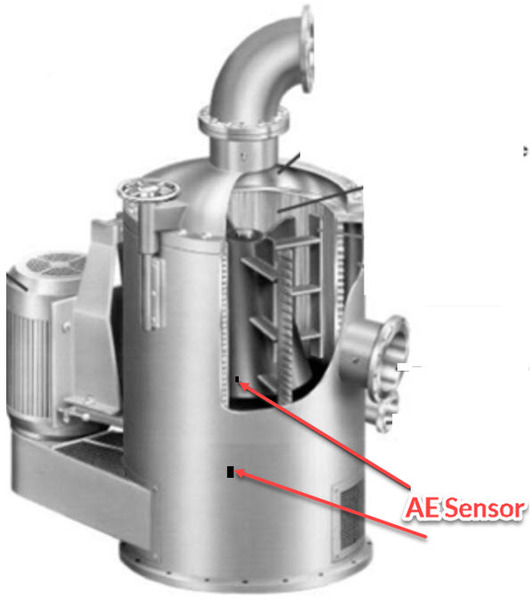
We are conducting research using acoustic emission (AE) sensors to measure waves through the machine body. Based on our previous experience and discussion with the industry, we convinced ourselves that acoustic signals contain rich information to identify issues in a refiner. For example, a refiner sounds different when there are issues, e.g., dull blades and too large/small gaps between blades. Another benefit of acoustic sensing is its non-destructive nature; unlike the force transducer, the acoustic sensors can be instrumented outside the refiner’s body and therefore minimally interrupt a regular operation of a refiner. We use a wide-bandwidth (4- 400,000 Hz) Sound and AE sensor.
We develop a high-speed data acquisition system to enable the implementation of real-time digital signal conditioning algorithms, such as to envelop detection. We also perform off-line signal processing, such as spectrogram, to capture time-varying spectra of the acoustic signals.
The acoustic data will be labeled based on their corresponding output pulp quality, e.g., good or bad, to form a “training set” to implement supervised learning techniques. We plan to collect the pulp quality data using Fiber Quality Analyzer (FQA) on-site for approximately a week. The result from supervised learning, i.e., classifier, will be used to implement a smart monitoring system that suggests the optimal time for blade changes and predicts the expected fiber quality.
Ongoing research…Read more
Temperature Sensor for Fast-Moving Surfaces
The temperature of a circular saw can be measured using a contact wireless temperature sensor. The saw temperature is a very important parameter to identify issues during cutting, determine the amount of water for cooling, the gaps between cuts, and monitoring the behavior of a saw. Read more on this Patent: Temperature sensor for fast-moving surface, US Patent App. 16/414,089, US20190353535A1
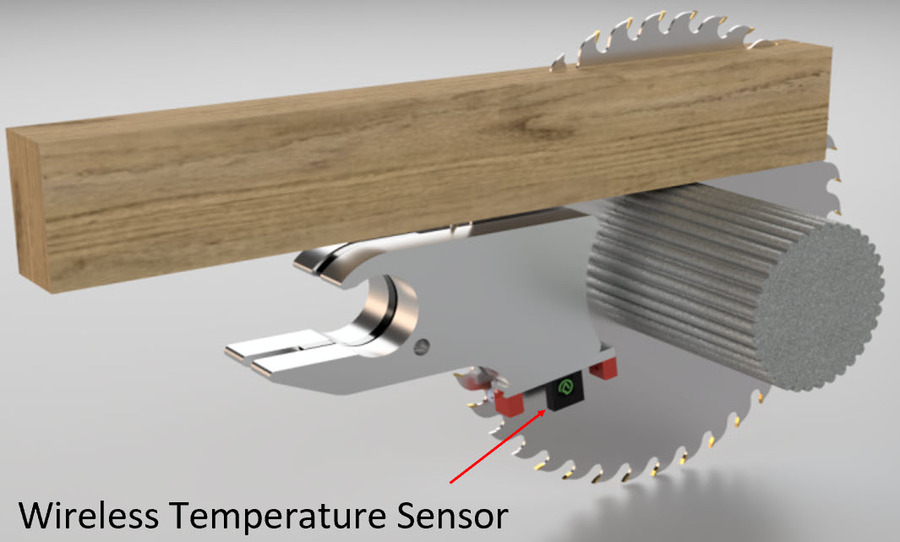
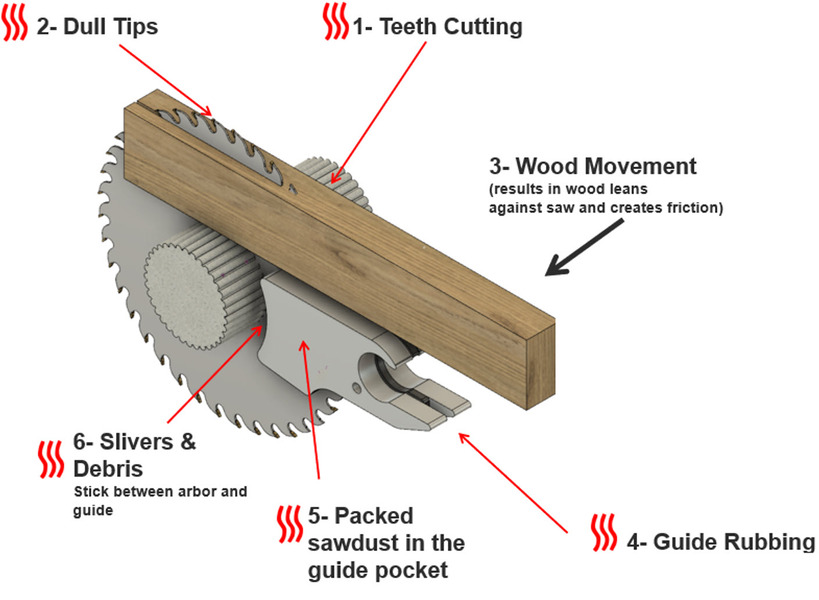
When sawing problems occur, as much data as possible is needed to understand how the saw responds under normal and upset conditions. The recent development of a circular saw temperature sensor makes the measurement of saw temperature possible. Several sawmill tests confirmed that monitoring saw temperature during sawing can provide useful information to diagnose sawing and guide lubrication issues.
A temperature sensor was designed and prototyped which enables real-time accurate temperature measurements of circular saw blades during cutting. These sensors provide real-time accurate temperature measurements of circular saw blades during cutting. The sensor wirelessly transmits the data to a base station where the values become available on the network. A monitoring application records the temperatures at each sensor at each saw over time. Read more on this Patent: Temperature sensor for fast-moving surface, US Patent App. 16/414,089, US20190353535A1
The sensors and their application were presented first in 2019 in Oregon, USA.
“Ahmad Mohammadpanah, IWMS23, International Wood Machining Seminar, University of Oregon, USA June 2019. “Critical Temperature of Circular Saws”. Access the paper
Applications of Spherical Parallel Manipulator
Parallel manipulators consist of separate serial chains connecting the fixed base to the moving platform. Typically, a parallel mechanism is said to be symmetrical if one actuator controls every limb and the location and the number of actuated joints in all the limbs are the same. The mechanism can produce a translation or spherical motion to a platform. The parallel robots can be equipped with hydraulic or pneumatic actuators.
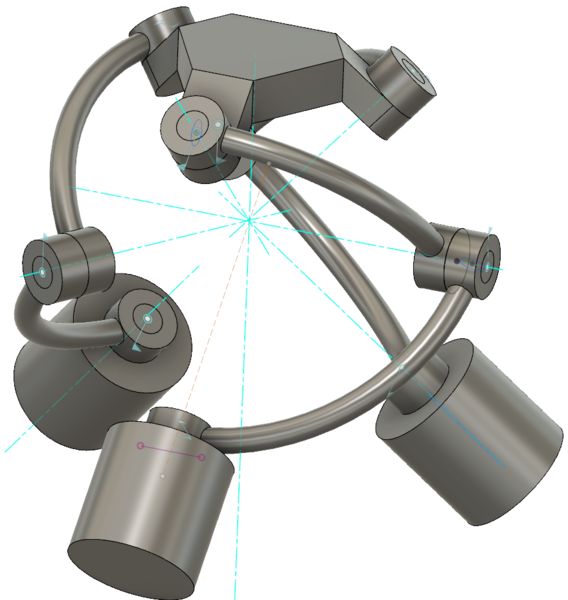
They have a robust construction and can move bodies of heavy masses and dimensions with high speeds. Compared with the serial robots, parallel mechanisms have some special characteristics: greater structural rigidity, higher orientation accuracy, functional stability, larger dynamic charge capacity and suitable position of the actuating systems.
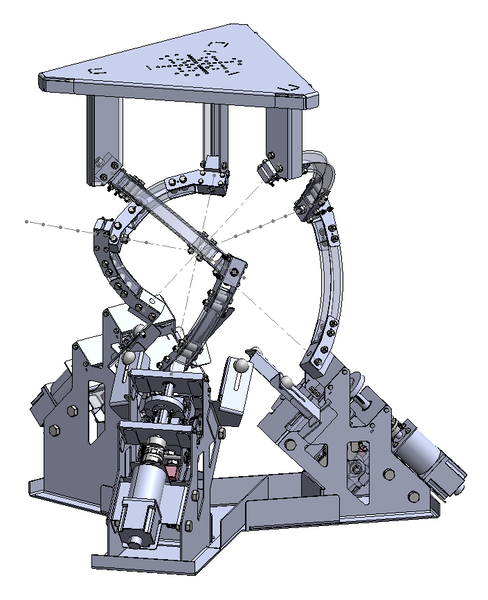
This mechanism has a plethora of applications in Bio-Medical Engineering, Military, Industrial Automation, fast pick-and-place operations, Precision machinery, High precision surface laser scanning, Orientation of Antenna, Orientation of solar panels, Orientation of high-speed cameras, tracking of high-speed objects, flight simulator, Micro-surgery, Remote Surgery, many applications in nuclear power plants, and manifold of other applications. Therefore, the research on this project can attract funds from government agencies and different industries.
I have been doing research on the dynamics analyses of this mechanism. So far, I have studied the equations of motions. I have also completed the simulation of the mechanism. Currently, a mechanical engineering student team at UBC is building the mechanism under my supervision. It will be used for conducting experimental tests.
The plan is to use the mechanism in SLS….
Ongoing research …